BUILDING AMERICA (BA) has been advocating the use of rigid foam sheathing insulation for years as a means to improve the home’s thermal envelope, by increasing R-value while minimizing thermal bridging in wood-framed walls.
Research by several teams has provided the critical scientific basis for acceptance of foam sheathing by the codes community, and resulted in best practices for installation to ensure thermal performance—as well as air barrier and drainage plane integrity. Exterior Insulating Sheathing Scenarios
In addition to rigid insulation best practices, adding insulating sheathing to the exterior of the assembly is a simple method of increasing the overall thermal resistance of the wall assembly beyond what is possible with cavity insulations, thereby increasing the overall efficiency of the house.
Adding one inch of insulating sheathing (R-5) will increase a 2’ x 6’ stud wall from an effective R-14.4 to an effective R-19.4. This represents an increase of 35 percent effective thermal resistance, with only 15 percent increase in the overall wall thickness.
In its Guide to Insulating Sheathing, BSC describes the use of exterior rigid insulation board in the enclosure assembly to act not only as insulation but also as the primary sheathing and, in certain areas, as the drainage plane and vapor control layer for the wall assembly (see Exterior Sheathing Profiles diagram.)
Proper Technique. If insulating sheathing is to serve as the drainage plane, all seams must be taped and flashing installed at all penetrations and openings.
General Considerations
Cladding attachment: All fasteners must be installed through to the studs, as insulating sheathing does not have adequate structural capacity both in shear and pull-out strength.
For Wall Sections 1 and 2, cladding systems such as traditional hard-coat stucco and acrylic stucco can be directly applied to the insulation board. Drained insulation boards (ones with vertical grooves cut in the back) or vertically textured (or profiled) housewraps are recommended, to ensure a drainage space behind the rigid board.
For Wall Sections 3 and 4, traditional hard-coat stucco (including thin brick and manufactured stone veneer) should NOT be installed without the addition of at least one layer of building paper or housewrap between the stucco renderings and the housewrap or drainage plane sheathing to act as a bond break.
Foundations connection: Continue the sheathing past the top edge of the foundation or basement wall to create a shingle lap with the foundation.
Advanced framing: The use of advanced framing with insulating sheathing can reduce the amount of materials in residential construction. Layout of the sheathing boards should minimize cutting and construction waste.
Cross bracing: Wall Systems 2, 3 and 4 require alternative methods of shear resistance, such as metal cross-bracing or inset shear panels.
Vapor management: Using impermeable insulating sheathing materials of adequate thickness can lower the condensation potential, and in some climates can allow for the elimination of the interior vapor control layer.
Moisture control
Cold climates: Use a more vapor-permeable insulating sheathing (such as EPS and unfaced XPS) on the exterior. Hot-humid climates: Use a more vapor impermeable sheathing on the exterior of the assembly (such as foil-faced polyisocyanurate and plastic film-faced XPS). Mixed-humid climates: The assembly needs to be protected from wetting from both the interior as well as the exterior. The drying can be predominantly to the exterior, the interior, or in both directions in a flow-through type assembly.
Resource: BSC’s Guide to Insulating Sheathing
Exterior Sheathing Profiles
Wall Section 1: Insulating Sheathing and Housewrap over Plywood or OSB: Insulating sheathing is installed on top of a layer of building paper or housewrap and wood sheathing.
Most durable assembly; drainage plane material is supported by the plywood sheathing and protected against wind loading and other environmental factors by the insulating sheathing.
Recommended in areas or high exposure and rainfall.
Wall Section 2: Insulation Sheathing and Housewrap over Wood Studs: Insulating sheathing is installed on top of a housewrap that is stretched over wood studs.
Housewrap drainage plane is protected from exterior elements (excessive wind loading and rain exposure).
Effective in most rainfall zones, though potentially not in high exposure locations.
More care is required during the installation of the housewrap and insulating sheathing.
Wall Section 3: Housewrap installed over Insulating Sheathing and Wood Studs: Housewrap is installed to the exterior of the insulating sheathing.
Insulating sheathing essentially replaces the plywood or OSB in a traditional wall assembly.
Housewrap is more exposed to exterior elements such as wind loading and moisture; may not be as durable as other approaches.
Fasteners used to install the housewrap must be able to penetrate all the way through the insulating sheathing and into the wood studs beyond.
Suitable for most rainfall zones.
Wall Section 4: Insulating Sheathing as the Drainage Plane: Insulating sheathing serves as the primary sheathing and drainage plane of the assembly.
Higher risk; should only be used in areas with limited rainfall and exposure, where rainwater management is not as critical.
All joints between the insulation boards must be designed to prevent water from penetrating past the exterior face of the insulation.
Vertical joints must be taped and sealed; if possible, use products with shingle laps or tongue and groove joints.
Polyethylene flashing should be installed at horizontal joints.
The Ideal Wall System In one study, Moisture and Structural Analysis for High Performance Hybrid Wall Assemblies, Building Science Corporation (BSC) analyzed several combinations of wall materials looking for an assembly that would provide the most effective thermal, air, moisture and water barrier systems, as well as sufficient structural strength. Using Building Energy Optimization (BEopt), thermal, hygrothermal and structural analysis, they came up with the optimal framed wall:
- 2’ x 6’ advanced framing with 1.5-inch closed-cell spray polyurethane foam in each stud bay
- 3 inches of cellulose insulation covered by 0.5-inch gypsum with latex paint finish
- Diagonal metal strapping on the exterior
- 1.5-inch foil-faced polyisocyanurate board insulation and exterior vertical wood strapping for cladding attachment.
This wall had the lowest associated incremental cost, lowest associated air-leakage condensation risk at less than 1 percent of the year in Minneapolis, the best structural performance—based on American Society for Testing and Materials (ASTM) E72—and the second-best annual energy savings at 34 percent in Minneapolis and 29 percent in New Orleans.
Veteran journalist Matt Power has reported on innovation and sustainability in housing for nearly three decades. An award-winning writer, editor, and filmmaker, he has a long history of asking hard questions and adding depth and context as he unfolds complex issues.
Exterior Foam Insulation: Best Practices
BUILDING AMERICA (BA) has been advocating the use of rigid foam sheathing insulation for years as a means to improve the home’s thermal envelope, by increasing R-value while minimizing thermal bridging in wood-framed walls.
Research by several teams has provided the critical scientific basis for acceptance of foam sheathing by the codes community, and resulted in best practices for installation to ensure thermal performance—as well as air barrier and drainage plane integrity. Exterior Insulating Sheathing Scenarios
In addition to rigid insulation best practices, adding insulating sheathing to the exterior of the assembly is a simple method of increasing the overall thermal resistance of the wall assembly beyond what is possible with cavity insulations, thereby increasing the overall efficiency of the house.
Adding one inch of insulating sheathing (R-5) will increase a 2’ x 6’ stud wall from an effective R-14.4 to an effective R-19.4. This represents an increase of 35 percent effective thermal resistance, with only 15 percent increase in the overall wall thickness.
In its Guide to Insulating Sheathing, BSC describes the use of exterior rigid insulation board in the enclosure assembly to act not only as insulation but also as the primary sheathing and, in certain areas, as the drainage plane and vapor control layer for the wall assembly (see Exterior Sheathing Profiles diagram.)
Proper Technique. If insulating sheathing is to serve as the drainage plane, all seams must be taped and flashing installed at all penetrations and openings.
General Considerations
Cladding attachment: All fasteners must be installed through to the studs, as insulating sheathing does not have adequate structural capacity both in shear and pull-out strength.
For Wall Sections 1 and 2, cladding systems such as traditional hard-coat stucco and acrylic stucco can be directly applied to the insulation board. Drained insulation boards (ones with vertical grooves cut in the back) or vertically textured (or profiled) housewraps are recommended, to ensure a drainage space behind the rigid board.
For Wall Sections 3 and 4, traditional hard-coat stucco (including thin brick and manufactured stone veneer) should NOT be installed without the addition of at least one layer of building paper or housewrap between the stucco renderings and the housewrap or drainage plane sheathing to act as a bond break.
Foundations connection: Continue the sheathing past the top edge of the foundation or basement wall to create a shingle lap with the foundation.
Advanced framing: The use of advanced framing with insulating sheathing can reduce the amount of materials in residential construction. Layout of the sheathing boards should minimize cutting and construction waste.
Cross bracing: Wall Systems 2, 3 and 4 require alternative methods of shear resistance, such as metal cross-bracing or inset shear panels.
Vapor management: Using impermeable insulating sheathing materials of adequate thickness can lower the condensation potential, and in some climates can allow for the elimination of the interior vapor control layer.
Moisture control
Cold climates: Use a more vapor-permeable insulating sheathing (such as EPS and unfaced XPS) on the exterior.
Hot-humid climates: Use a more vapor impermeable sheathing on the exterior of the assembly (such as foil-faced polyisocyanurate and plastic film-faced XPS).
Mixed-humid climates: The assembly needs to be protected from wetting from both the interior as well as the exterior. The drying can be predominantly to the exterior, the interior, or in both directions in a flow-through type assembly.
Resource: BSC’s Guide to Insulating Sheathing
Exterior Sheathing Profiles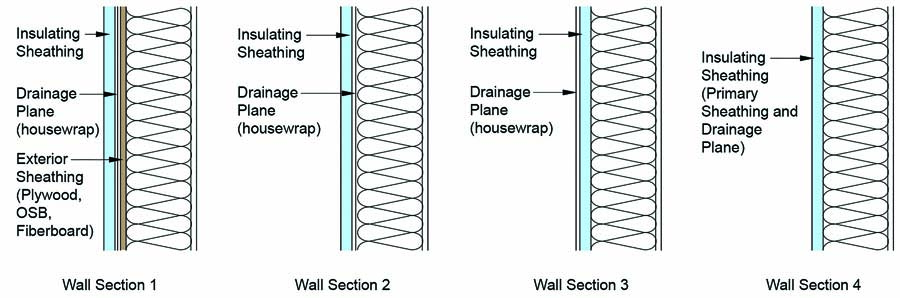
Wall Section 1: Insulating Sheathing and Housewrap over Plywood or OSB: Insulating sheathing is installed on top of a layer of building paper or housewrap and wood sheathing.
Wall Section 2: Insulation Sheathing and Housewrap over Wood Studs: Insulating sheathing is installed on top of a housewrap that is stretched over wood studs.
Wall Section 3: Housewrap installed over Insulating Sheathing and Wood Studs: Housewrap is installed to the exterior of the insulating sheathing.
Wall Section 4: Insulating Sheathing as the Drainage Plane: Insulating sheathing serves as the primary sheathing and drainage plane of the assembly.
The Ideal Wall System
In one study, Moisture and Structural Analysis for High Performance Hybrid Wall Assemblies, Building Science Corporation (BSC) analyzed several combinations of wall materials looking for an assembly that would provide the most effective thermal, air, moisture and water barrier systems, as well as sufficient structural strength. Using Building Energy Optimization (BEopt), thermal, hygrothermal and structural analysis, they came up with the optimal framed wall:
- 2’ x 6’ advanced framing with 1.5-inch closed-cell spray polyurethane foam in each stud bay
- 3 inches of cellulose insulation covered by 0.5-inch gypsum with latex paint finish
- Diagonal metal strapping on the exterior
- 1.5-inch foil-faced polyisocyanurate board insulation and exterior vertical wood strapping for cladding attachment.
This wall had the lowest associated incremental cost, lowest associated air-leakage condensation risk at less than 1 percent of the year in Minneapolis, the best structural performance—based on American Society for Testing and Materials (ASTM) E72—and the second-best annual energy savings at 34 percent in Minneapolis and 29 percent in New Orleans.
By Matt Power, Editor-In-Chief
Veteran journalist Matt Power has reported on innovation and sustainability in housing for nearly three decades. An award-winning writer, editor, and filmmaker, he has a long history of asking hard questions and adding depth and context as he unfolds complex issues.