Combining spray foam with Neopor sheathing, this wall system achieves R-34 with two-by-four framing.
One of the challenges of moving the needle on home energy efficiency has been resistance to change on the part of many builders, who have always built homes the same way, with conventional 2x4 stick framing.
But material shortages associated with the pandemic have created at least a temporary opening for so-called “system” approaches to wall construction.
Manufacturers such as BASF have shifted to more nuanced combinations of materials.
The HP+ system, for example, consists of a “sandwich” of insulation, around a structurally braced 2x4 structure. Why “braced?” Because instead of relying on the sheer strength of structural panel such as OSB, this wall system leapfrogs the usual limitations of R-value for 2x4 framed walls. By combing two high-performance insulators, it also greatly reduces exterior finish costs, with the application of a one-coat final finish stucco.
Building science expert Steve Easley notes that this system can also be used with 2x6 framing to achieve insulating values of R-42. “That’s getting into the range of Passivhaus,” he points out, “where walls range from about R-40 to R-60.”
The mechanics of the HP+ system include three main components:
Rigid Foam: On the exterior, creating a full thermal break, is a 1-inch panel of Neopor, a graphite-enhanced, rigid foam board.
Closed-Cell Spray Foam: The 2x4 cavities are filled with spray-in closed cell foam, (WALLTITE HP+), from BASF.
Stucco: Finally, the sheathing is coated with with an air- and water-resistant resilient coating called ENERSHIELD.
Methods for bracing the HP+ wall system are fairly straightforward. Lateral let-in bracing or steel straps can remain in place permanently. Other so called “in-plane bracing” may be used only when setting the wall. This is because the closed cell WALLTITE spray foam adds a lot of shear strength after it sets.
Brad Townsend, head of Residential Market Development for Construction for BASF, notes that builders will soon see stricter codes, such as California’s new Title 24 Zero Net Energy requirement. Systems like HP+ making getting to zero much easier.
Ready For Foam. Staging walls to receive HP+ insulation and sheathing typically requires additional bracing.
“Their challenge, I think is that they don’t know how to sell a better envelope,” he says. “They think they can’t compete if they add any cost, but a builder’s largest competitor isn’t the other builder in town, it’s the resale market.
“The appraisal market needs to catch up to building technology,” he adds. “A spray foam system like HP+ means you’ve got more value: a safer and healthier home that you can control. It gives you the ability to really isolate the indoor environment, to control air leakage and sound and energy use.”
Townsend adds that the financial payback with a high-performance envelope is almost immediate, compared with a conventional wall/roof system.
“Let’s just take one scenario,” he says. “Say it costs me $3,000 more to build my next home this way. At today’s mortgage rates, that’s $15 per month added to a 30-year mortgage. But you’re saving $85 a month on energy costs for the life of the home. So out of the gate the product is paying you back $70 a month.”
The HP+ technical docs note that the wall system works with Advanced Framing (Optimum Value Engineering) if desired, although “Additional studs or blocking may be required by the cladding manufacturer, or for window and door frame bearing.”
Veteran journalist Matt Power has reported on innovation and sustainability in housing for nearly three decades. An award-winning writer, editor, and filmmaker, he has a long history of asking hard questions and adding depth and context as he unfolds complex issues.
Hybrid Wall System Drastically Reduces Energy Bills
Combining spray foam with Neopor sheathing, this wall system achieves R-34 with two-by-four framing.
One of the challenges of moving the needle on home energy efficiency has been resistance to change on the part of many builders, who have always built homes the same way, with conventional 2x4 stick framing.
But material shortages associated with the pandemic have created at least a temporary opening for so-called “system” approaches to wall construction.
Manufacturers such as BASF have shifted to more nuanced combinations of materials.
The HP+ system, for example, consists of a “sandwich” of insulation, around a structurally braced 2x4 structure. Why “braced?” Because instead of relying on the sheer strength of structural panel such as OSB, this wall system leapfrogs the usual limitations of R-value for 2x4 framed walls. By combing two high-performance insulators, it also greatly reduces exterior finish costs, with the application of a one-coat final finish stucco.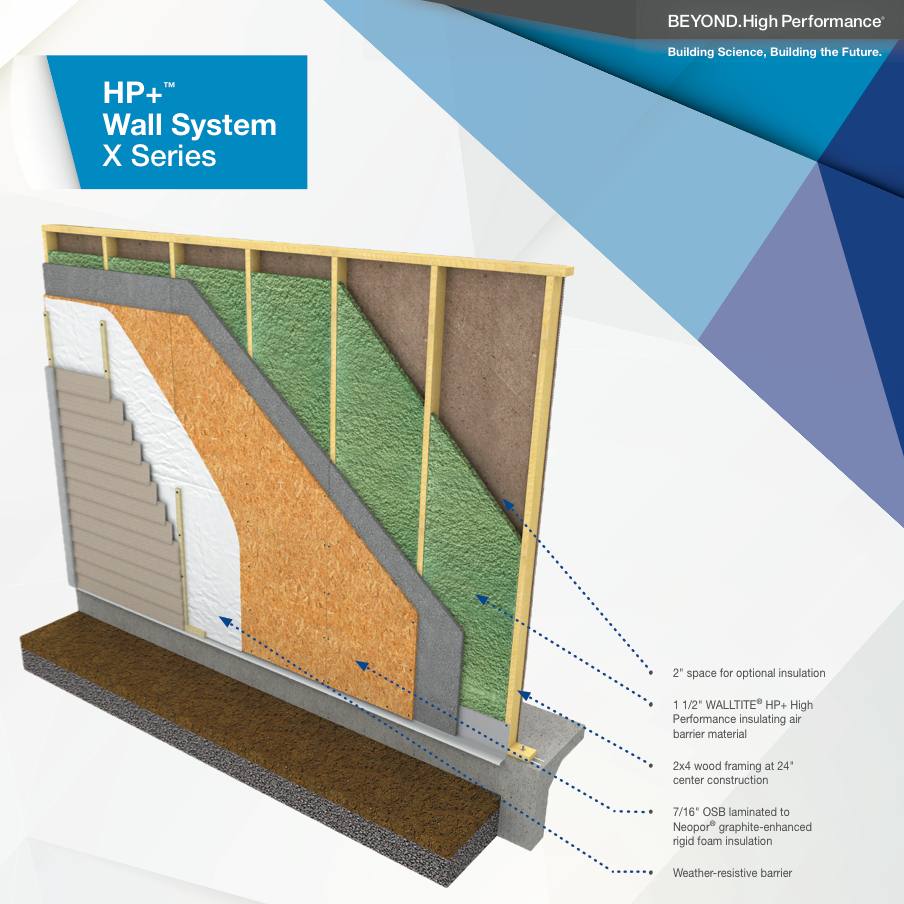
Building science expert Steve Easley notes that this system can also be used with 2x6 framing to achieve insulating values of R-42. “That’s getting into the range of Passivhaus,” he points out, “where walls range from about R-40 to R-60.”
The mechanics of the HP+ system include three main components:
Methods for bracing the HP+ wall system are fairly straightforward. Lateral let-in bracing or steel straps can remain in place permanently. Other so called “in-plane bracing” may be used only when setting the wall. This is because the closed cell WALLTITE spray foam adds a lot of shear strength after it sets.
Brad Townsend, head of Residential Market Development for Construction for BASF, notes that builders will soon see stricter codes, such as California’s new Title 24 Zero Net Energy requirement. Systems like HP+ making getting to zero much easier.
Ready For Foam. Staging walls to receive HP+ insulation and sheathing typically requires additional bracing.
“Their challenge, I think is that they don’t know how to sell a better envelope,” he says. “They think they can’t compete if they add any cost, but a builder’s largest competitor isn’t the other builder in town, it’s the resale market.
“The appraisal market needs to catch up to building technology,” he adds. “A spray foam system like HP+ means you’ve got more value: a safer and healthier home that you can control. It gives you the ability to really isolate the indoor environment, to control air leakage and sound and energy use.”
Townsend adds that the financial payback with a high-performance envelope is almost immediate, compared with a conventional wall/roof system.
“Let’s just take one scenario,” he says. “Say it costs me $3,000 more to build my next home this way. At today’s mortgage rates, that’s $15 per month added to a 30-year mortgage. But you’re saving $85 a month on energy costs for the life of the home. So out of the gate the product is paying you back $70 a month.”
The HP+ technical docs note that the wall system works with Advanced Framing (Optimum Value Engineering) if desired, although “Additional studs or blocking may be required by the cladding manufacturer, or for window and door frame bearing.”
Technical Specifications for HP+ can be found here.
By Matt Power, Editor-In-Chief
Veteran journalist Matt Power has reported on innovation and sustainability in housing for nearly three decades. An award-winning writer, editor, and filmmaker, he has a long history of asking hard questions and adding depth and context as he unfolds complex issues.Also Read