These five innovations offer ways to stay ahead of disruption in the building industry.
Two key points about disruption. One, it happens. And not only does it happen, but also it happens with exponentially increasing frequency and magnitude. That’s because data, software, and technology innovations are enabling vast opportunities to deliver better user experiences at lower cost.
The second point is critical: When disruption happens, the two choices are to either adapt or get left behind. The market is littered with lost jobs and failed businesses in the wake of innovation. I often talk about the large array of enterprises eliminated when the automobile disrupted the horse and buggy at the turn of the 20th Century.
A more recent example of accelerated disruption is how quickly the smartphone introduced in 2007 has been replacing dozens of technologies: landline, camera, cam-recorder, radio, GPS, alarm clocks, wristwatch, timer, portable music players, eBook reader, calculator, watches, flashlights, newspapers, photo album and the list goes on.
This disruption is graphically depicted in Figure 1 below for just one of these technologies, the camera. Today film camera sales are negligible and digital camera sales have decreased over 90 percent from its peak in 2010.
Figure 1: The Age of Innovation Acceleration – Cameras
The resulting home of the future will blow away everything we’re building today with a transformative user experience. Zero energy is an important part of this home of the future. Without question, zero has left the station. Consider the following developments:
The International Energy Conservation Code (IECC) has been rapidly increasing in rigor. The latest 2021 IECC is effectively a zero energy enclosure code that exceeds the Department of Energy Zero Energy Ready Home current program requirements and serves as the baseline in the forthcoming 2024 program requirements.
Seven states are planning or currently implementing zero energy or zero energy ready codes including California, New Jersey, New Mexico, New York, Oregon, Puerto Rico and Washington.
Eighteen states have adopted 100 percent clean energy or renewable energy policies that typically include zero energy buildings.
Since 2020 there has been a 190 percent growth in total homes voluntarily certified to zero energy and zero energy ready programs in the U.S. and Canada. This includes a 440 percent growth in single-family homes with over 67,000 certified units in 2022.
Zero energy ready homes are being offered for $148 per square foot by a leading manufactured home company. This establishes zero energy in the lowest cost housing segment.
For the next ten years starting in 2023, the 45L tax credit will provide builders $5,000 for each single-family home and $1,000 for each multi-family unit certified to Zero Energy Ready Home.
60% of global investors surveyed plan to adopt Environmental, Social and Governance (ESG) criteria. This is already influencing the largest publicly owned builders to engage in ESG reporting and leverage high-performance certifications to strengthen their environmental scores.
And last, but not least, readers of this column know the heavy emphasis I place on optimizing user experience. Zero takes the homeowner experience to the next level including ultra-low energy bills, enhanced comfort, low-maintenance, safety, health, and resilience. And as an industry, we just need to be better at translating this value.
These developments are a clear signal it’s time for all builders, architects, and housing programs to begin adapting and not get left behind the zero train. The key to optimizing success with zero is to deliver better performance for lower cost.
To that end, there are five highly under-utilized innovations that offer impressive faster, better and cheaper benefits compared to business-as-usual options.
Five High-Performance Home Innovations
1. Unvented Attics. The most egregious interface in the home enclosure is between the attic and ceiling below. This is because it is exposed to the most extreme temperature differential during summer, a constant stack effect pressure difference, extensive air barrier challenges (e.g., knee walls, dropped and raised ceiling, shafts, and wind baffles), and extensive air sealing challenges (e.g., penetrations, duct boots, access panels, and drywall to top plate).
As a result, the attic/ceiling interface is the most important for controlling air, thermal, and moisture flow. However, a standard red line test tracing the air barrier across the entire enclosure reveals a missing top-side air barrier (see Figure 2). This compromises efficiency, comfort and creates the worst location for HVAC equipment.
Figure 2: Redline air barrier test showing missing air barrier at top side of attic insulation in vented attic
Home performance can be substantially improved with unvented attics most commonly with structural insulated panels (SIPs) as the roof structure or spray-foam insulation installed at the roof rafters.
The resulting benefits for unvented attic benefits include:
2. Precast Concrete Foundations: Compared to typical poured-in-place concrete foundations, precast concrete foundations are produced offsite in large panels and installed in the field. They use a ribbed configuration that significantly reduces the amount of concrete required.
In addition, rigid foam insulation (e.g., typically R-10) is installed in the plant along the interior face including the concrete ribs for a complete thermal break assembly. The ribs are covered with a metal channel so interior drywall can be attached without a framed wall. And last, the assembled panels act like an effective bond-beam and do not require a concrete footing. Figure 3 shows a comparison of pour-in-place and precast concrete foundations.
Figure 3: Comparison of pour-in-place and precast concrete foundations
Meticulous field work is needed to ensure a perfectly level gravel bed for precast concrete panels. However, this will substantially improve accuracy for all construction above the foundation.
The resulting benefits for precast concrete foundations include:
3. Structural Insulated Panels (SIPs). Traditional framing represents 150-plus-year-old enclosure technology with only minor incremental innovations. Maybe it’s time for change. SIPs are sandwich panels that are fabricated in a factory. Two skins, typically OSB or plywood, are pressed and glued to a foam panel, most commonly expanded polystyrene or extruded polystyrene (see Figure 4). These panels can typically be made as large as 24 ft. x 9 ft. in size.
Figure 4: Traditional framing compared to SIPs construction
The resulting benefits of SIPs compared to traditional framing include:
4. Aerosol Air Sealing. Manual air sealing uses field labor working in diverse weather conditions to seal over a half-mile of cracks and hundreds of penetrations in typical construction. All of this can be automated with a system that uses computer-controlled blowers to pressurize the house with an aerosol-based sealant mixture.
The aerosol under pressure accelerates through any holes or cracks where the sealant is deposited until fully sealed. Results are monitored and measured in real time to ensure the air sealing target is reached. Figure 5 shows a comparison between manual and aerosol air sealing.
Figure 5: Manual air sealing compared to aerosol air sealing
The resulting benefits of aerosol air sealing compared to manual air sealing include:
5. Plug-and-Play Ducts. Quality design and installation with conventional HVAC duct systems have been a serious problem. One study revealed 67 to 100 percent of systems tested had significant duct leakage and 50 to 93 percent of systems had incorrect air flow.
Maybe once again it is time for a change. In this case, a plug-and-play duct system that easily snaps together and is automatically air-tight. It is substantially simpler than a conventional HVAC duct layout using one small duct, approximately 2.5 inches in diameter, that is home-run from a manifold type cap on the plenum to a supply grill in each room (see Figure 6).
Figure 6: Plug-and-play duct system
Each small duct supplies approximately 25 cfm of flow. The number of supply ducts run to each room is determined by the total cfm required. For instance, a room requiring 70 cfm of conditioned air flow would have three of the ducts run to supply grills spaced around the room.
The resulting benefits of a plug-and-play HVAC duct system compared to conventional duct systems include:
Recommendation
Here’s the problem. The impressive benefits to improved performance, cost savings, risk reduction, quality, and process associated with new innovations are rarely integrated into the bidding process. Thus, business-as-usual technologies have an unfair advantage on top of an incredibly change-resistant industry.
As discussed at the beginning of this article, the zero train has left the station. It’s incumbent on all high-performance home builders and professionals to get to high-performance faster, better and cheaper. That begins by looking at the true cost of innovation including all of the difficult to measure benefits.
Hopefully this article is a good start. But help is on the way. I’ll be introducing a number of true-cost bidding tools in 2023 to help make more informed decisions.
Sam Rashkin’s two-decade career as a licensed architect includes serving on national steering committees for the U.S. Green Building Council (USGBC)’s LEED for Homes, Green Builder Media’s Green Builder Guidelines, the Environmental Protection Agency (EPA)’s WaterSense label, and EPA’s Indoor airPLUS label. He has partnered with Green Builder Media to develop the Housing 2.0 program , which empowers building professionals to design and construct higher-performance, healthier and more-sustainable homes at a fraction of the cost.
Zero-Energy Housing: 5 Faster, Better, and Cheaper Innovations
These five innovations offer ways to stay ahead of disruption in the building industry.
Two key points about disruption. One, it happens. And not only does it happen, but also it happens with exponentially increasing frequency and magnitude. That’s because data, software, and technology innovations are enabling vast opportunities to deliver better user experiences at lower cost.
A more recent example of accelerated disruption is how quickly the smartphone introduced in 2007 has been replacing dozens of technologies: landline, camera, cam-recorder, radio, GPS, alarm clocks, wristwatch, timer, portable music players, eBook reader, calculator, watches, flashlights, newspapers, photo album and the list goes on.
This disruption is graphically depicted in Figure 1 below for just one of these technologies, the camera. Today film camera sales are negligible and digital camera sales have decreased over 90 percent from its peak in 2010.
Figure 1: The Age of Innovation Acceleration – Cameras
Which brings us to sustainable housing. Disruption is finally coming to the industry most resistant to change. I’ll refer you to my book, “Housing 2.0” for a detailed discussion of the five crises imposing huge pain on the housing industry and the four market-ready innovations to relieve that pain.
The resulting home of the future will blow away everything we’re building today with a transformative user experience. Zero energy is an important part of this home of the future. Without question, zero has left the station. Consider the following developments:
These developments are a clear signal it’s time for all builders, architects, and housing programs to begin adapting and not get left behind the zero train. The key to optimizing success with zero is to deliver better performance for lower cost.
To that end, there are five highly under-utilized innovations that offer impressive faster, better and cheaper benefits compared to business-as-usual options.
Five High-Performance Home Innovations
1. Unvented Attics. The most egregious interface in the home enclosure is between the attic and ceiling below. This is because it is exposed to the most extreme temperature differential during summer, a constant stack effect pressure difference, extensive air barrier challenges (e.g., knee walls, dropped and raised ceiling, shafts, and wind baffles), and extensive air sealing challenges (e.g., penetrations, duct boots, access panels, and drywall to top plate).As a result, the attic/ceiling interface is the most important for controlling air, thermal, and moisture flow. However, a standard red line test tracing the air barrier across the entire enclosure reveals a missing top-side air barrier (see Figure 2). This compromises efficiency, comfort and creates the worst location for HVAC equipment.
Figure 2: Redline air barrier test showing missing air barrier at top side of attic insulation in vented attic
Home performance can be substantially improved with unvented attics most commonly with structural insulated panels (SIPs) as the roof structure or spray-foam insulation installed at the roof rafters.
The resulting benefits for unvented attic benefits include:
2. Precast Concrete Foundations: Compared to typical poured-in-place concrete foundations, precast concrete foundations are produced offsite in large panels and installed in the field. They use a ribbed configuration that significantly reduces the amount of concrete required.
In addition, rigid foam insulation (e.g., typically R-10) is installed in the plant along the interior face including the concrete ribs for a complete thermal break assembly. The ribs are covered with a metal channel so interior drywall can be attached without a framed wall. And last, the assembled panels act like an effective bond-beam and do not require a concrete footing. Figure 3 shows a comparison of pour-in-place and precast concrete foundations.
Figure 3: Comparison of pour-in-place and precast concrete foundations
Meticulous field work is needed to ensure a perfectly level gravel bed for precast concrete panels. However, this will substantially improve accuracy for all construction above the foundation.
The resulting benefits for precast concrete foundations include:
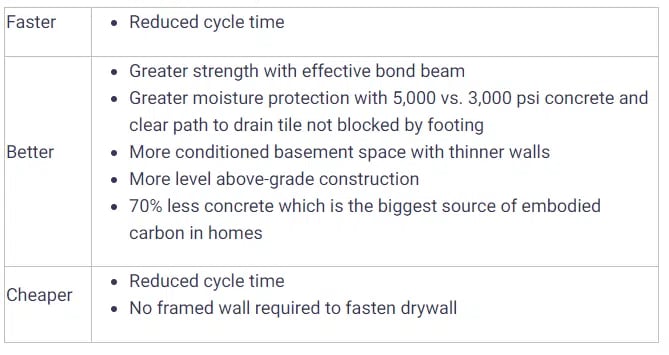
3. Structural Insulated Panels (SIPs). Traditional framing represents 150-plus-year-old enclosure technology with only minor incremental innovations. Maybe it’s time for change. SIPs are sandwich panels that are fabricated in a factory. Two skins, typically OSB or plywood, are pressed and glued to a foam panel, most commonly expanded polystyrene or extruded polystyrene (see Figure 4). These panels can typically be made as large as 24 ft. x 9 ft. in size.Figure 4: Traditional framing compared to SIPs construction
The resulting benefits of SIPs compared to traditional framing include:
The aerosol under pressure accelerates through any holes or cracks where the sealant is deposited until fully sealed. Results are monitored and measured in real time to ensure the air sealing target is reached. Figure 5 shows a comparison between manual and aerosol air sealing.
Figure 5: Manual air sealing compared to aerosol air sealing
The resulting benefits of aerosol air sealing compared to manual air sealing include:
5. Plug-and-Play Ducts. Quality design and installation with conventional HVAC duct systems have been a serious problem. One study revealed 67 to 100 percent of systems tested had significant duct leakage and 50 to 93 percent of systems had incorrect air flow.
Maybe once again it is time for a change. In this case, a plug-and-play duct system that easily snaps together and is automatically air-tight. It is substantially simpler than a conventional HVAC duct layout using one small duct, approximately 2.5 inches in diameter, that is home-run from a manifold type cap on the plenum to a supply grill in each room (see Figure 6).
Figure 6: Plug-and-play duct system
Each small duct supplies approximately 25 cfm of flow. The number of supply ducts run to each room is determined by the total cfm required. For instance, a room requiring 70 cfm of conditioned air flow would have three of the ducts run to supply grills spaced around the room.
The resulting benefits of a plug-and-play HVAC duct system compared to conventional duct systems include:
Recommendation
Here’s the problem. The impressive benefits to improved performance, cost savings, risk reduction, quality, and process associated with new innovations are rarely integrated into the bidding process. Thus, business-as-usual technologies have an unfair advantage on top of an incredibly change-resistant industry.
As discussed at the beginning of this article, the zero train has left the station. It’s incumbent on all high-performance home builders and professionals to get to high-performance faster, better and cheaper. That begins by looking at the true cost of innovation including all of the difficult to measure benefits.
Hopefully this article is a good start. But help is on the way. I’ll be introducing a number of true-cost bidding tools in 2023 to help make more informed decisions.
This Housing 2.0 presentation is sponsored by: Jinko Solar, LP Building Solutions, Mitsubishi Electric , Panasonic, Schneider Electric and Sunnova.
By Sam Rashkin
Sam Rashkin’s two-decade career as a licensed architect includes serving on national steering committees for the U.S. Green Building Council (USGBC)’s LEED for Homes, Green Builder Media’s Green Builder Guidelines, the Environmental Protection Agency (EPA)’s WaterSense label, and EPA’s Indoor airPLUS label. He has partnered with Green Builder Media to develop the Housing 2.0 program , which empowers building professionals to design and construct higher-performance, healthier and more-sustainable homes at a fraction of the cost.Also Read