First in a series of blogs that will explain what hundreds of people have already learned about Housing 2.0, which is now entering its fourth year. Come along and see what your peers have learned.
If there’s one thing the homebuilding industry is not historically known for, it’s change. We highlight this in the first Housing 2.0 workshop when we compare photographs from two different residential job sites, separated primarily by 140 years. It is staggering to see how similar the photos are.
Men building a wood-frame structure. Lumber strewn on the dirt around the outside of the house. Imagine for a minute if that were true of the transportation industry. Horse manure shoveler would still be a job!
Change is exactly what the industry needs right now, and for multiple reasons. One is the trades; specifically, attracting new talent. Availability of labor is one of the biggest concerns amongst builders. The $64 million-dollar question is: How do we bring a new generation of laborers into the homebuilding industry before we start to see the elder statesmen and stateswomen call it a career? Because if it doesn’t happen soon, we’ll really see what a labor shortage looks like.
Affordability is another admittedly complex issue facing the industry. Part of that is where we choose to live. Density has its benefits, but it also means a lot of people are competing for relatively little land.
While we’re not suggesting we pave Montana, simple economics will tell you that if supply is low and demand is high, prices will be high. Part of the equation is labor rates. Many Americans live paycheck to paycheck. Setting aside poor, self-inflicted financial choices, the salaries of many blue-collar workers have been unfairly suppressed.
While we’re starting to see that get corrected in certain states, rising labor rates also raises the cost of goods. It’s a vicious cycle, and not unique to the homebuilding industry. It affects housing affordability nonetheless. Thankfully, one thing we can do to combat this is doing all we can to lower the operational costs of homes.
We can also look at the productivity of the homebuilding process. Here, there is room for massive improvement via automation. Taking a more manufactured approach would also raise quality (by eliminating weather) and reduce cycle times.
Production builders certainly know that time is money. What if all builders could take advantage of similar speeds? We’ve seen such a transformation in the automobile industry. The assembly lines of 100 years ago don’t look anything like those of today… and we make better cars that run longer and cleaner.
In addition to these problems, we also discuss solutions. Concepts, practices and techniques that can demonstrably reduce construction costs, which improves affordability.
To learn more about those, well… you’ll need to watch the video below:
Mike Collignon, author of our Code Watch and Housing 2.0 Program Manager, is Executive Director and Co-Founder of the Green Builder Coalition, a not-for-profit association dedicated to amplifying the voice of green builders and professionals to drive advocacy and education for more sustainable homebuilding practices.
Future of Housing with Certainty: Adapt or Be Left Behind
First in a series of blogs that will explain what hundreds of people have already learned about Housing 2.0, which is now entering its fourth year. Come along and see what your peers have learned.
If there’s one thing the homebuilding industry is not historically known for, it’s change. We highlight this in the first Housing 2.0 workshop when we compare photographs from two different residential job sites, separated primarily by 140 years. It is staggering to see how similar the photos are.
Men building a wood-frame structure. Lumber strewn on the dirt around the outside of the house. Imagine for a minute if that were true of the transportation industry. Horse manure shoveler would still be a job!
Change is exactly what the industry needs right now, and for multiple reasons. One is the trades; specifically, attracting new talent. Availability of labor is one of the biggest concerns amongst builders. The $64 million-dollar question is: How do we bring a new generation of laborers into the homebuilding industry before we start to see the elder statesmen and stateswomen call it a career? Because if it doesn’t happen soon, we’ll really see what a labor shortage looks like.
Affordability is another admittedly complex issue facing the industry. Part of that is where we choose to live. Density has its benefits, but it also means a lot of people are competing for relatively little land.
While we’re not suggesting we pave Montana, simple economics will tell you that if supply is low and demand is high, prices will be high. Part of the equation is labor rates. Many Americans live paycheck to paycheck. Setting aside poor, self-inflicted financial choices, the salaries of many blue-collar workers have been unfairly suppressed.
While we’re starting to see that get corrected in certain states, rising labor rates also raises the cost of goods. It’s a vicious cycle, and not unique to the homebuilding industry. It affects housing affordability nonetheless. Thankfully, one thing we can do to combat this is doing all we can to lower the operational costs of homes.
We can also look at the productivity of the homebuilding process. Here, there is room for massive improvement via automation. Taking a more manufactured approach would also raise quality (by eliminating weather) and reduce cycle times.
Production builders certainly know that time is money. What if all builders could take advantage of similar speeds? We’ve seen such a transformation in the automobile industry. The assembly lines of 100 years ago don’t look anything like those of today… and we make better cars that run longer and cleaner.
In addition to these problems, we also discuss solutions. Concepts, practices and techniques that can demonstrably reduce construction costs, which improves affordability.
To learn more about those, well… you’ll need to watch the video below: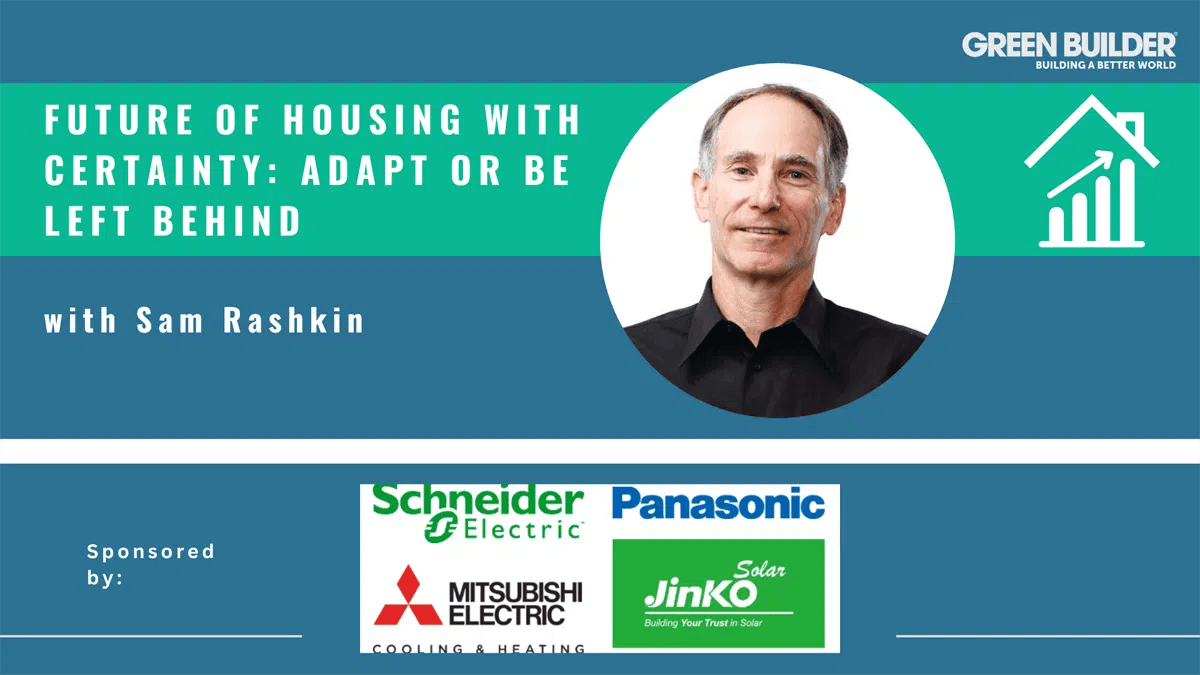
If you want to take a step back and read about the overall Housing 2.0 program, click here .
By Mike Collignon
Mike Collignon, author of our Code Watch and Housing 2.0 Program Manager, is Executive Director and Co-Founder of the Green Builder Coalition, a not-for-profit association dedicated to amplifying the voice of green builders and professionals to drive advocacy and education for more sustainable homebuilding practices.Also Read